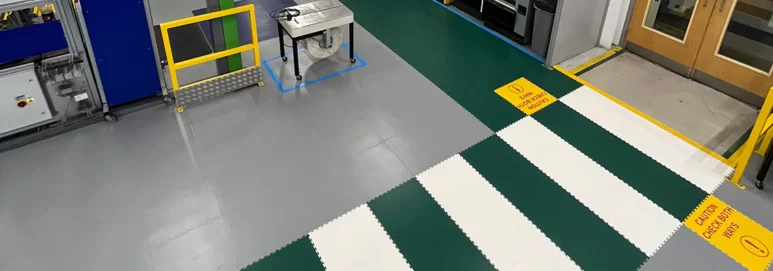
Warehouse flooring types explained – Which option is right for you?
April 3, 2025With several warehouse flooring types available, it can be hard to decide which is best for your business.
Whether you are laying a new floor or upgrading an old one, your choice impacts everything from daily operations to long-term costs. This decision is particularly important given today’s demanding warehouse operations and workplace health and safety regulations.
Let’s take a closer look at the most popular warehouse flooring options and examine their performance, along with their pros and cons. Using these insights, you can make a more informed decision that balances both immediate needs and long-term value.
Let’s explore
- Bare concrete flooring
- Epoxy resin floors
- Painted, sealed or polished floors
- Vinyl or PVC sheet flooring
- Why modular flooring stands out
- Making the right choice for your warehouse
- Conclusion
Concrete flooring (the traditional choice)
As most warehouses in the UK already have concrete subfloors, many businesses choose to operate on concrete. When properly installed, concrete provides a solid foundation that can support heavy machinery, racking systems and constant forklift traffic.
However, many warehouse managers don’t find out about the disadvantages of concrete until after a sustained period of use.
Protecting the concrete in a leased building is often an overlooked consideration. Many landlords will contractually require concrete subfloors to be repaired at the end of lease, often leading to costly repairs upon exit.
Advantages of Concrete Flooring
- Cost-effective as most premises already have bare concrete subfloors
- Impressive load bearing capacity making it ideal for heavy equipment and racking
- Long lifespan potential of over 20 years with proper maintenance
- Compatible with most warehouse applications across various industries
Disadvantages of Concrete Flooring
- Excessive dust production (can compromise stock, machinery and air quality)
- Poor thermal properties mean warehouses are colder, and can increase heating costs
- Prone to cracking under temperature changes and heavy loads
- Low noise absorption creates echoing working environments
- Costly to repair when damage occurs, often requiring disruptive remedial work
- High maintenance, including regular cleaning and repeated resealing
- Hard surface, impacting worker comfort (anti-fatigue mats can be used to overcome this, but they add an additional expense)
Epoxy (better than basic concrete, but with downsides)
Epoxy coatings provide a step up from bare concrete. Its improved aesthetics and surface protection make this a more attractive option. Many warehouse managers choose this resin flooring option to gain extra benefits without completely replacing existing concrete floors.
Advantages of Epoxy Flooring
- Chemical and stain resistance (ideal for warehouses handling corrosive materials)
- Better light reflection enhancing workplace visibility
- Seamless surface that supports hygiene requirements and reduces cleaning time
- Concrete protection (extends the life of the underlying floor)
Disadvantages of Epoxy Flooring
- Installation downtime caused by epoxy resin curing times can disrupt operations for 3 to 7 days
- Limited lifespan in high-traffic areas means reapplication is inevitable
- Potential slipping hazard (especially in areas exposed to moisture)
- Professional installation required (increasing costs)
- Performance and durability is dependent on proper surface preparation
- Costly failures and high repair bills if application is sub-standard
- Prone to moisture damage, including groundwater issues that are common in warehouses
Painted, sealed or polished concrete – an economical middle ground
For warehouse managers operating with tighter budgets, painted, sealed, or polished concrete flooring offers a compromise solution. It addresses some of the shortcomings of concrete without significant initial investment. However, where consideration is given to long term value, repeated application of paint or sealants do not provide the best value for money.
Advantages
- Quicker application process than epoxy, reducing operational disruption
- Dust reduction improves workplace conditions
- Enhanced visual appearance creates a more professional environment
- Simple implementation of safety markings and zone designations
- Relatively low initial investment compared to comprehensive flooring systems
Disadvantages
- Rapid wear in high-traffic routes leads to frequent touch-ups and maintenance
- Limited protection against impacts and heavy use
- Poor resistance to chemicals and spillages potentially leading to permanent staining
- Short effective lifespan increases long-term costs through repeated applications
- Minimal improvements to comfort or thermal properties
Vinyl or PVC sheet flooring
Vinyl flooring finds its niche in specific warehouse applications where hygiene, comfort, or aesthetic requirements take priority over durability concerns.
Advantages
- Superior hygiene properties make it suitable for food preparation or pharmaceutical settings
- Better underfoot comfort reduces staff fatigue during long shifts
- Good slip-resistance options enhance safety in wet areas
- Attractive appearance for customer-facing warehouse sections
- Effective noise reduction creates a more pleasant working environment
Disadvantages
- Poor puncture resistance makes it vulnerable to damage from dropped items
- Limited weight tolerance makes it unsuitable for heavy machinery or high-point loads
- Challenging repairs can often lead to extensive section replacements
- Adhesive-dependent installation causes extended operational downtime
- Higher maintenance requirements than alternative industrial flooring solutions
- Prone to damage from pallet trucks and other warehouse equipment
Interlocking floor tiles (a modular warehouse flooring solution)
Interlocking modular floor systems represent enhancements in warehouse flooring technology. They offer businesses a flexible solution to address many of the limitations found in more traditional options.
Advantages of Interlocking Flooring
- Rapid install with zero downtime, so facilities continue running during install
- No need for surface prep, it can even be installed over damaged concrete
- Save on extensive subfloor repair costs
- Impressive durability against heavy traffic, point loads and impact damage
- 20+ year lifespan
- Simple DIY installation mitigates professional fitting costs
- Easy maintenance and cleaning with standard industrial equipment
- Excellent resistance to oils, chemicals, and acids that are common in industrial environments
- Superior thermal insulation, creating warmer workspaces and reducing heating costs
- Effective noise reduction to improve the working environment
- Quick and economical repairs as damaged tiles can be replaced individually
- Easy to reuse and relocate, providing flexibility for changing business needs
- No VOCs and reduces dust to help to maintain air quality standards
- Built-in anti-slip properties enhance workplace safety
- Easily create work zones, highlight danger areas, or identify safe walkways
Disadvantages of Interlocking Flooring
- Higher initial investment than basic concrete treatments (offset by lower lifetime costs)
- Height difference at edges mean transition strips may be required in some installations
- Colour fading is possible in areas with direct sunlight exposure over extended periods
- Temperature differences sometimes require tiles to be glued to the subfloor to prevent expansion
Making the right choice for your warehouse
When selecting warehouse flooring for your facility, several factors should influence your decision:
- Operational requirements, for example traffic, equipment weights and the nature of your operations
- Environmental considerations such as moisture and the local climate
- Health and safety compliance (flooring choice impacts your ability to meet regulations)
- Long-term value as well as installation costs. Consider lifetime expenses such as maintenance, repairs, and potential replacements
- Installation impact (operational losses / disruption that installation may cause)
- Environmental goals – consider the environmental impact of your flooring choice. This includes longevity and the potential for end-of-life recycling. Greener choices are better for business by showing your company cares about the health of the planet
Why modular flooring stands out for modern warehouses
For most warehouse applications, interlocking modular flooring systems offer the most comprehensive solution to common challenges. The unique advantages of systems like Ecotile interlocking flooring address specific concerns that warehouse managers face.
- Subfloor protection, as modular tiles create a protective barrier for the concrete substrate from damage. This extends the life of the underlying floor and prevents costly concrete repairs.
- Versatile to diverse environments, since high-quality interlocking tiles are not affected by moisture issues commonly found in warehouse settings, unlike concrete and epoxy resin flooring.
- Minimal disruption: Downtime means lost revenue. The ability to install new flooring without stopping operations is highly valuable. When downtime losses are offset against higher upfront costs, interlocking floor tiles offer a more cost-effective solution overall.
- Lower lifetime costs: While the upfront costs may be higher than more basic options, reduced maintenance, simple repairs, and a longer lifespan often result in better long-term value.
- Staff wellbeing benefits: Improved thermal and acoustic properties create a better working environment. This can enhance productivity and reduce absence rates. Interlocking tiles are also available in anti-fatigue options to further alleviate joint discomfort.
- Futureproofing: As the only truly flexible and reusable option, modular flooring adapts to changing business needs. Whether relocating or changing your warehouse layout, or introducing mobile robots, it offers a versatile solution without the need for complete replacement.
- Warehouse managers and business owners looking for a practical, durable and cost-effective flooring solution will find that interlocking floor systems offer benefits that traditional flooring options simply cannot match.
Conclusion
Warehouse managers and business owners looking for a practical, durable and cost-effective flooring solution will find that interlocking floor systems offer benefits that traditional flooring options simply cannot match.
When considering the full life cycle, from installation and maintenance to eventual replacement, the benefits of modular flooring solutions become increasingly clear.
In fact, interlocking floor tiles are the only flooring option you can take away with you when you move business premises. What’s more, some companies (including Ecotile) even offer a recycling service for a greener solution.
In contrast, options like bare concrete flooring come with their own set of issues including harsher working conditions and expensive repairs. While epoxy resin flooring may seem like the logical choice due to its popularity and aesthetic appeal, its lengthy curing times, slip resistance and costly repairs can make it an expensive option in the long-run.
The best advice we can offer those looking to install or replace a commercial or industrial floor is to speak to a trusted flooring specialist. They will be able to guide you through all the options and advise on installation times.
If you’re interested in finding out more about Ecotile for your warehouse, get in touch for a free consultation.
David Bryant-Pugh is sales and marketing manager of Ecotile Flooring. A Member of the Chartered Institute of Marketing (MCIM), David divides his time between creating strategy and tactics for the modular flooring business, and meeting customers to better understand their needs and specific marketplace. Operating across multiple industry sectors (every business has a floor, right!) David’s experience ranges from manufacturing to retail, and everything in between.
Prior to Ecotile, David managed the marketing team at Argos for Business. He previously built a wealth of experience in the foodservice and construction industries as marketing lead. You can find David on LinkedIn